Servo Motor Injection Molding Machine(90Ton-4000Ton)
With our cutting-edge Servo Motor Injection Molding Machines, spanning from 90 to 4000 ton, developed to suit all your plastic injection molding needs, welcome to the world of advanced production. Our machines provide unmatched efficiency, dependability, and versatility thanks to cutting-edge technology and precise engineering, ensuring that your manufacturing processes reach new levels of productivity and perfection. With our sector-leading solutions, which provide top-tier performance for all your manufacturing needs, embrace the future of injection molding.
- Fast Shipping
- Support OEM&ODM
- TOP Quality
- Professional Service
DESCRIPTION
Our product portfolio, which covers loads between 130 and 4000 ton, providing a comprehensive solution for all of your injection molding needs. These devices, which make use of servo motor technology, raise the bar for production efficiency with their unrivalled precision, speed, and energy economy. Our Servo Motor Molding Machines are the perfect choice for your manufacturing operations, whether you’re producing little components or big-ticket items. They are made to operate superbly and to be dependable and versatile. You can see the future of injection molding with our cutting-edge solutions, which are designed to boost your production and grow your company. Here are a few qualities to consider.
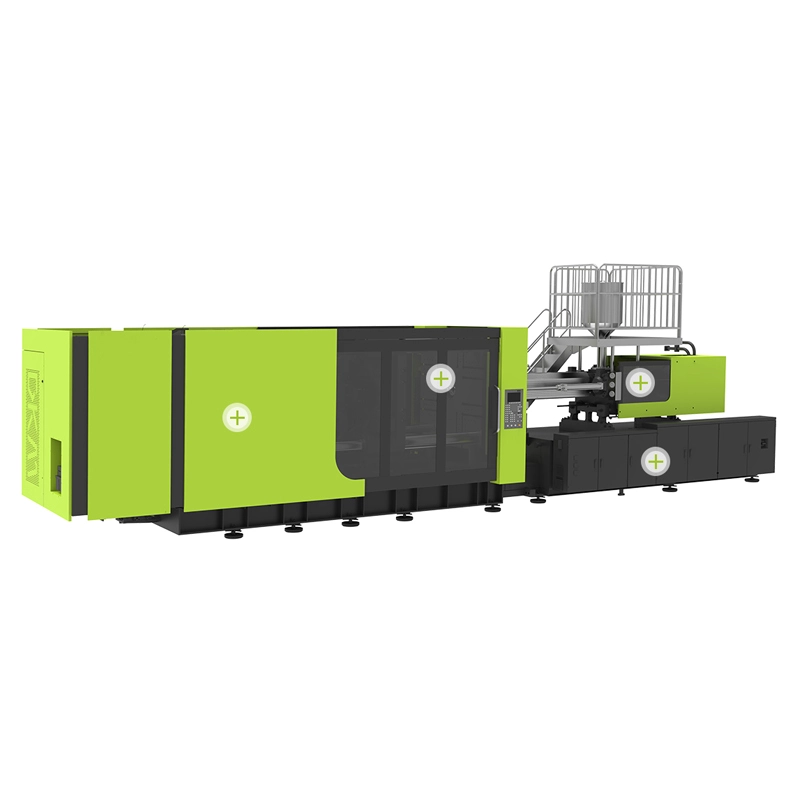
Wide range of tonnage options available, from 130 tons to 4000 tons
Utilizes advanced servo motor technology for precise and efficient operation
High-speed injection for improved productivity
Energy-efficient design reduces power consumption
Exceptional precision and repeatability for consistent quality
Versatile machine capable of handling various types of plastics
Robust construction for durability and longevity
User-friendly interface for easy operation and monitoring
Advanced control system for precise parameter adjustment
Safety features to ensure operator protection
Optional customization and configuration to meet specific production requirements
Servo Motor Injection Molding Machine Specification
180SV
250SV
350SV
450SV
550SV
650SV
850SV
1150SV
1350SV
1650SV
2250SV
2800SV
3350SV
Servo Motor Injection Molding Machine in operations
Servo Motor Injection Molding Machines showcase their remarkable capabilities and efficiency. The integration of servo motor technology enables precise and dynamic control over the injection process, resulting in consistent and high-quality outputs. These machines offer rapid injection speeds, minimizing cycle times and maximizing productivity. Their energy-efficient design also optimizes power use, cutting down on operating expenses. They are appropriate for a variety of sectors and applications because to their adaptability, which allows them to accommodate a wide range of plastic materials. Operators will appreciate the user-friendly interface and advanced control system, allowing for easy parameter adjustments and monitoring. Safety features are also incorporated to ensure a secure working environment. Whether you require small-scale production or large-scale manufacturing, our servo motor plastic machine delivers exceptional performance and reliability, empowering you to meet your production goals efficiently and effectively.
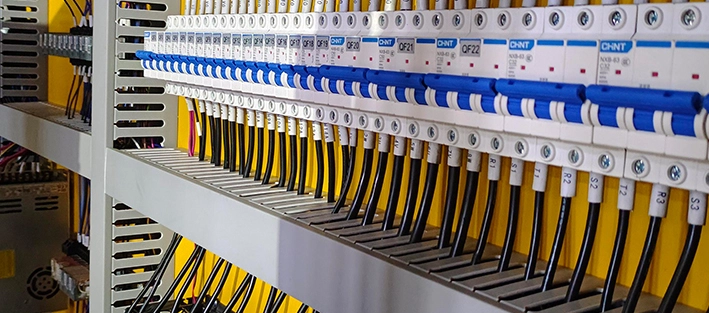
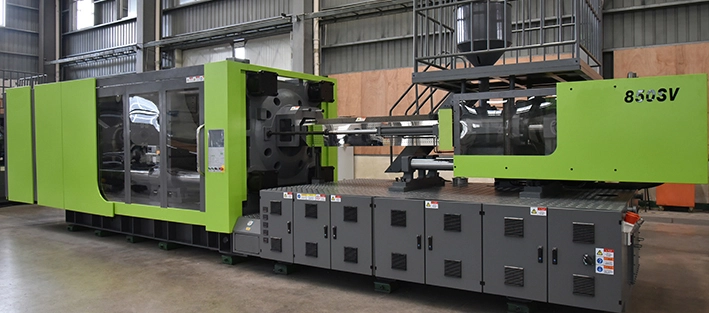
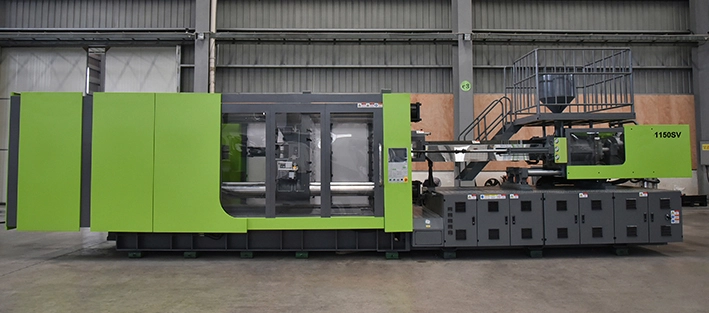
Using Guidelines:
Whether you are a beginner or an experienced user, you can follow the following steps to achieve the best results.
Step 1
Preparing the Machine
a. Make sure the machine is tidy and free of any debris or impediments.
b. Verify that all safety barriers and locks are in place and working properly.
c. Verify that the required mold, raw material, and auxiliary equipment are ready for use.
Step 2
Powering On
a. Connect the machine to a reliable power source.
b. Switch on the main power supply and auxiliary systems (such as the hydraulic system and cooling system).
Step 3
Setting Up the Mold
a. Carefully mount the mold onto the machine’s platens, following the manufacturer’s guidelines.
b. Securely fasten the mold using appropriate clamping mechanisms.
c. Ensure that the mold alignment is correct and that all mold components are properly installed.
Step 4
Adjusting Machine Parameters
a. Access the machine’s control panel or interface.
b. Set the desired injection parameters, such as injection speed, pressure, and holding time, based on the specific requirements of the product and material being used.
c. Configure the temperature settings for the barrel, nozzle, and mold heating zones.
Step 5
Loading Raw Material
a. Prepare the raw material by ensuring it is properly dried and free from contamination.
b. Open the machine’s hopper and pour the required amount of material into it.
c. Close the hopper securely to prevent material spillage.
Step 6
Running the Machine
a. Initiate the automatic or manual mode based on your preference and experience.
b. Start the machine’s operation, and closely monitor the injection process for any abnormalities.
c. Adjust the parameters as needed to achieve the desired product quality and production efficiency.
Step 7
Post-Injection Process
a. Allow the injection molding process to complete as per the specified cycle time.
b. Once the injection is complete, activate the mold opening mechanism to release the molded part.
c. Carefully remove the part from the mold, ensuring proper handling to avoid damage or injury.
Step 8
Machine Maintenance and Shutdown
a. After completing the production run, clean the machine thoroughly to remove any residual material or contaminants.
b. Perform routine maintenance tasks as recommended by the manufacturer, such as lubricating moving parts and inspecting hydraulic systems.
c. Switch off the machine, auxiliary systems, and main power supply.
Advantages of using Servo Motor Injection Molding Machine(80Ton-4000Ton):
The advantages of using a Servo Motor Injection Molding Machine (ranging from 80 tons to 4000 tons) are numerous and can significantly enhance your manufacturing operations. Here are the key advantages in detail:
Energy Efficiency
Precision and Consistency
Faster Cycle Times
Enhanced Process Control
Quieter Operation
Versatility
Reduced Maintenance
Improved Safety
User-Friendly Interface
Longevity and Reliability
Servo motor technology ensures optimal energy consumption by adjusting the motor speed based on the required load. It results in significant energy savings compared to traditional hydraulic systems, leading to lower operating costs and a smaller carbon footprint.
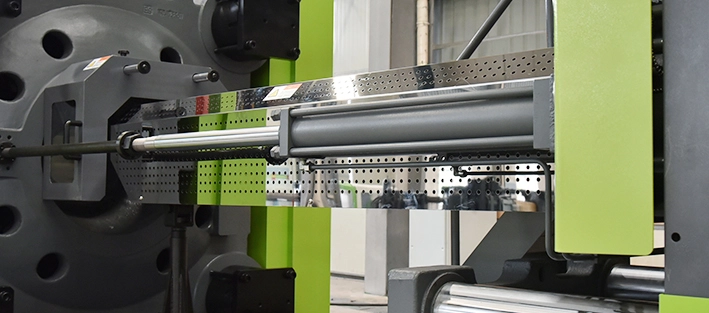
Machine Specifications:
Familiarize yourself with the specific specifications of the machine you are operating, including its tonnage range (80 tons to 4000 tons) and other relevant parameters such as maximum injection pressure, injection speed, and mold opening stroke. Understanding these specifications will help you optimize your production process.
Servo Motor Technology:
Gain a comprehensive understanding of the servo motor technology employed in the machine. Servo motors offer precise control, energy efficiency, and improved responsiveness, enabling enhanced performance and cost savings compared to traditional hydraulic systems.
Mold Compatibility:
Ensure that the mold you are using is compatible with the machine’s specifications. Consider factors such as mold size, clamping force requirements, and any specific mold features or accessories needed for proper installation and operation.
Material Compatibility:
Different Plastic injection molding machines are designed to process specific types of plastic materials. Verify that the machine is suitable for the type of material you intend to use. Additionally, understand the material’s melt temperature, flow characteristics, and any specific processing requirements to optimize the injection process.
Machine Operation:
Understand the operating procedures and controls specific to the machine you are working with. Learn how to set and adjust parameters such as injection speed, pressure, holding time, and temperature settings. Additionally, become familiar with the machine’s control panel, interface, and any available automation features.
Maintenance and Troubleshooting:
Regular maintenance is essential for the smooth operation of the machine. For normal maintenance chores like lubrication, filter changes, and hydraulic system check, according to the manufacturer’s instructions. Learn how to identify and fix any problems that might occur while operating by being familiar with standard troubleshooting techniques.
Training and Resources:
Ensure that operators receive appropriate training on the operation, maintenance, and safety aspects of the machine. Utilise the tools at your disposal, such as user manuals, technical assistance, and training courses offered by the machine’s manufacturer, to expand your understanding and competence.
Related products
-
PET Series Injection Molding Machine(170T-470T)
Injection Molding Machine -
Toggle Hydraulic Injection Molding Machine(90T-650T)
Injection Molding Machine -
Direct Press Type Injection Molding Machine(130T-2800T)
Injection Molding Machine -
All Electric Injection Molding Machine(90T-460T)
Injection Molding Machine